Medical device parts manufacturing services
We hope to provide you with the best customized processing and the best service.
Committed to achieving the highest machining accuracy and adhering to the strictest standards.
From a single prototype to the production of the largest batch of components, providing full-size inspection reports.
Advantages of Sumitech factory precision machining medical parts
1. Precision manufacturing capability: High precision equipment (such as five axis CNC, laser cutting, micrometer level detectors) can process tolerances up to ± 0.005mm.
2. Strict quality and compliance system: Certification: ISO 13485, Full process traceability system, compatibility testing, and sterile packaging validation.
3. Deep cultivation experience in the medical industry: providing long-term OEM services to the top 10 medical device companies worldwide, with a defect rate of less than 0.1% and a on-time delivery rate of 98%.
4. Customization and rapid response: The flexible production line supports small batches/urgent orders (72 hour sample delivery), and the technical team provides one-stop services from design optimization to mass production. Material expertise: Titanium alloys PEEK、 Patent for surface treatment technology of medical grade stainless steel and other materials. Cost optimization: Reduce customer unit costs through process innovation (such as eliminating secondary processing steps)
Sumitech has been dedicated to medical parts processing for 15 years, serving over 200 global medical device companies and safeguarding life and health through precision manufacturing.

cnc medical
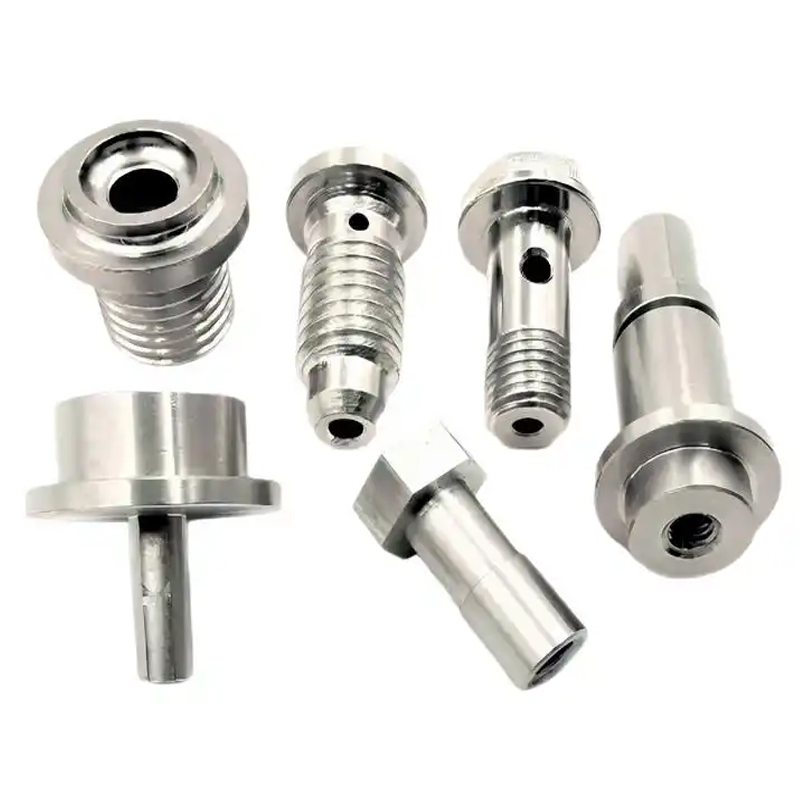
medical cnc machining
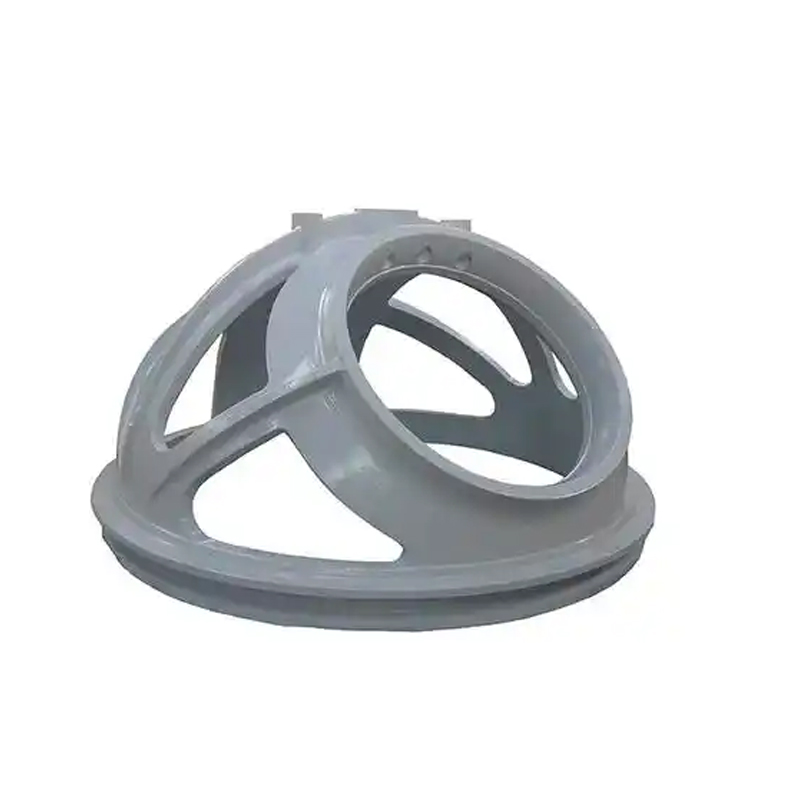
cnc machining for medical
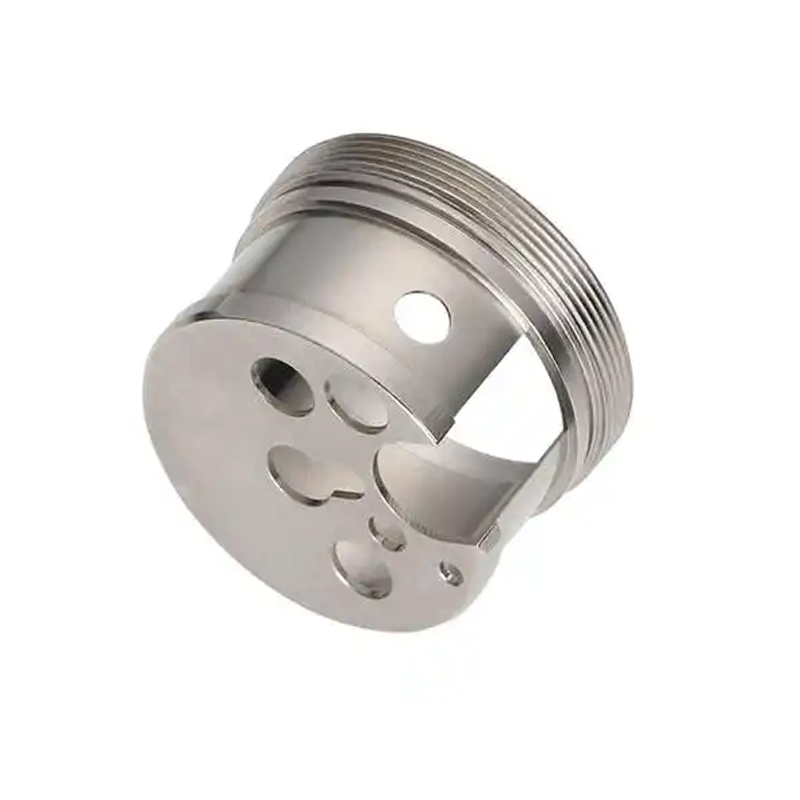
cnc machining medical
cnc medical parts
medical device machining
medical device cnc machining
cnc medical devices
cnc machining medical parts
medical machining services
cnc medical parts manufacturing
machining medical parts
medical cnc machining services
medical device precision machining
medical precision machining
PEEK Medical industry part
We can use these common machining process manufacture and customize medical equipment and instruments.
CNC (Computer Numerical Control) machining is a process that uses computer-controlled machinery to accurately cut and shape materials. In the medical device industry, CNC machining is commonly used for manufacturing metal components, casings, brackets, and precision parts.
Injection molding involves injecting molten plastic material into molds, which then cool and solidify to form the required medical device parts and components. In the medical device industry, injection molding is commonly used for manufacturing plastic casings, connectors, syringes, and handles.
3D printing technology enables the direct transformation of digital designs into three-dimensional objects by building them layer by layer. In the medical device industry, 3D printing can be used for manufacturing complex-shaped instrument parts, models, and customized medical devices.
Sheet metal fabrication involves processes such as cutting, bending, punching, and welding of thin metal sheets to manufacture casings, brackets, and panels for medical devices. Sheet metal fabrication provides high precision and complex-shaped components.
Precision machining techniques include micro-machining, grinding, milling, and drilling, used for manufacturing high-precision and intricate components in medical devices. These machining techniques ensure the accuracy, quality, and performance of the instruments.
Surface treatment of medical devices may include electroplating, anodizing, coating, and polishing. These treatments can enhance the corrosion resistance, appearance quality, and cleanliness of the instruments.
Do you need a project quotation? Contact us now via phone, email, or contact form