Precision cnc milling/cnc turning service
- Maintain the strictest tolerance of ± 0.002 mm during the production process.
- Timely delivery within 3 days or less.
- Save over 60% of costs.
- Can machining over 200 types of materials, including metal and plastic.
- From single prototype to mass production.
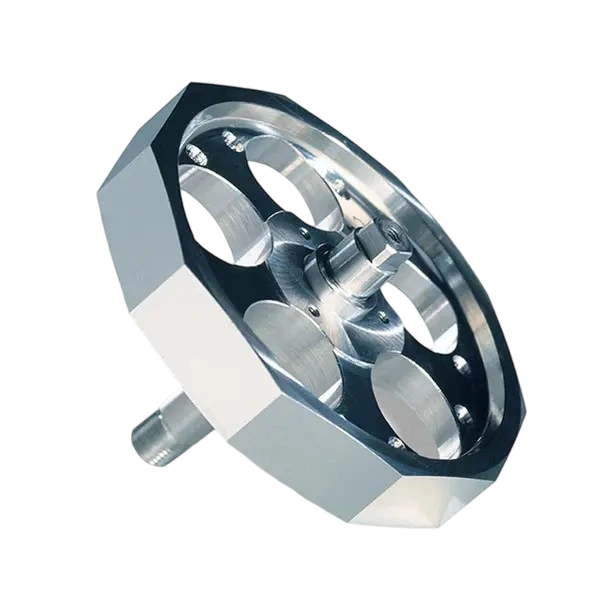
CNC milling/cnc turning case presentation
Various materials and shapes can be precisely customized for processing
We specialize cnc milling materials
1、 Metal materials
Steel category
Carbon steel, alloy steel, stainless steel (such as 316L), ductile iron, etc., suitable for processing automotive parts (gearbox housings) and medical implants.
High temperature resistant alloys (such as Inconel 718, Hastelloy) are used for aerospace turbine blades and energy equipment impellers.
Light metals and alloys
Aluminum alloy (6061, 5052), titanium alloy, suitable for lightweight parts (aviation accessories, consumer electronics radiators).
Copper alloys (such as brass and bronze) are used for connectors and precision electronic components.
Other metals
Nickel based alloys and duplex stainless steel are used for valve components in corrosion-resistant and high-temperature environments.
2、 Non metallic materials
Engineering plastics
PEEK (biocompatible material), nylon ABS, Used for medical equipment and lightweight structural components.
Polyoxymethylene (POM) and ultra-high molecular weight polyethylene (UHMW) are suitable for wear-resistant and low friction scenarios.
Composite materials
Carbon fiber and glass fiber reinforced materials are used for lightweight components in aerospace and automotive industries.
Other materials
Graphite, used for molds and special industrial parts (cutting parameters need to be controlled to prevent cracking).
3、 Special Materials and Processing Challenges
Hard material:
Hard alloy, requiring the use of high hardness cutting tools (such as diamond coated milling cutters).
High temperature materials:
Nickel based alloys require cooling techniques (such as dynamic cooling) to prevent tool overheating during processing.
Brittle materials:
Graphite needs to optimize cutting parameters (low feed, high speed) to reduce edge breakage.
The diversity of milling materials makes it suitable for a wide range of fields, from precision medical components to large industrial parts. The specific process requires adjusting the cutting tools and parameters according to the material characteristics. Contact us for a project evaluation plan.Customized products include:aerospace cnc milling,aerospace milling,arbor cnc milling,circular pocket milling,cnc 6040 milling aluminium,cnc machining turning,cnc micro milling,cnc milling carbon fiber,cnc milling gears,cnc milling turning,cnc milling product,copper cnc milling,flutes milling,milling carbon fiber sheet,modul cnc milling.
Sumitech milling advantages
1. The company has high-end equipment and multi axis technology.
Equipment model: Five axis linkage CNC milling machine (such as DMG MORI, MAZAK), machining center (such as HAAS, Makino).
Processing capability: Processing of complex surfaces, thin-walled parts, deep cavity structures, and irregular parts, supporting difficult to cut materials such as titanium alloys and high-temperature alloys.
Technical parameters: positioning accuracy (such as ± 0.003mm), surface roughness (Ra ≤ 0.8 μ m).
2. Ability to implement complex processes
Multi process integration: One clamping process completes composite processes such as drilling, boring, tapping, and contour machining.
Customized solutions: Provide process optimization for special needs such as molds, aerospace parts, medical implants, etc.
3. Accuracy and stability guarantee
Testing equipment: laser interferometer, profilometer, roughness tester.
Process control: Real time tool wear monitoring, temperature compensation system (to reduce thermal deformation errors).
Certification standards: ISO 9001, AS9100 (Aerospace), ISO 13485 (Medical).
4. Efficiency and Flexible Production
Quick mold changing system: Modular fixture design reduces mold changing time by 30% -50%.
Batch production: Automated pallet exchange system, supporting 24-hour continuous processing.
5. Industry specific solutions
Automotive mold: High smoothness surface treatment, suitable for die-casting/injection mold requirements.
Using a five axis high-speed milling machine (spindle speed 24000 RPM), the mirror surface machining of the mold cavity (Ra ≤ 0.4 μ m) is achieved, reducing the subsequent polishing process and shortening the delivery time by 20%. Processing large mold frames for automotive die-casting mold enterprises, with a flatness error of ≤ 0.02mm/m2, resulting in a 15% increase in customer product yield.
Aerospace: Lightweight structural processing (such as honeycomb structures, topology optimized parts).
Equipped with a five axis machining center with a constant temperature cooling system, capable of machining titanium alloy structural parts with a deformation of less than 0.01mm, suitable for key components such as aircraft wing ribs and engine brackets. Record key dimensional data packages throughout the entire process, comply with AS9100 traceability requirements, and support customer aviation material certification.
Medical devices: Precision machining of biocompatible materials such as titanium alloys and PEEK.
Precision micro milling technology (with a minimum tool diameter of 0.1mm) is used to complete the processing of porous structures in orthopedic implants, with a porosity error of less than 3%, accelerating patient bone fusion.
Provide demand
We can achieve your idea